Neues Rittal-Werk in Haiger ist die größte Investition der Unternehmensgeschichte
Ohne Digitalisierung nicht wettbewerbsfähig
„Mit diesem Werk schaffen wir einen komplett neuen Weltstandard für unsere Branche und weit darüber hinaus.“ So begrüßte Prof. Friedhelm Loh, Inhaber und Vorstandsvorsitzender der Friedhelm Loh Group, die anwesenden Journalisten bei der Vorstellung des neuen Werks zur Fertigung von Kompaktschaltschränken und Kleingehäusen. Im mittelhessischen Haiger wurde mit 250Mio.€ die größte Gesamtinvestition der Firmengeschichte getätigt.
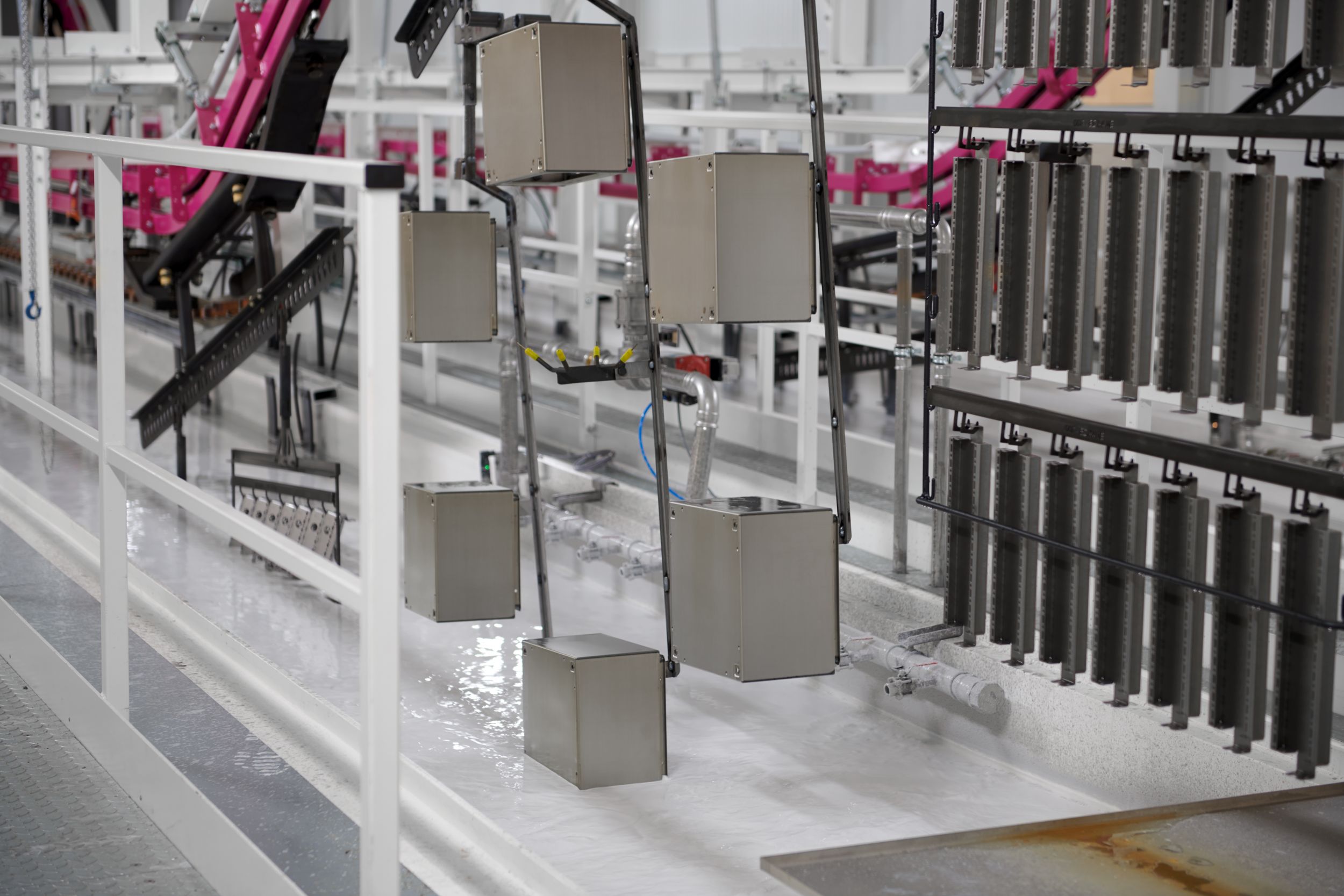
Die neue Produktionsstätte für Kleingehäuse und Kompaktschaltschränke in Haiger ist ein Paradebesipiel für eine nach Industrie-4.0-Maßstäben ausgerichtete Fertigung. (Bild: Rittal GmbH & Co. KG)
Durch die hochautomatisierte Produktionssteuerung im Verbund mit dem globalen Distributionszentrum wird das Werk zu einem zentralen Glied in der digitalisierten Auftragsabwicklung und zum Garanten für die Verfügbarkeit des Serienportfolios mit Zubehör. „Das Werk wird vollständig nach hocheffizienten Industrie-4.0-Strukturen ausgerichtet“, betonte Loh. Das neue Werk bietet 290 Arbeitsplätze. In den Fabrikhallen werden bald mit mehr als 100 neuen Hightech-Maschinen und Anlagenkomponenten auf 24.000m² hochautomatisiert rund 9.000 AX Kompaktschaltschränke und KX Kleingehäuse pro Tag gefertigt. Dafür wird das Werk rund 35.000 Tonnen Stahl pro Jahr verarbeiten. Im Produktionsprozess stellt sich der Maschinenpark in Haiger zunehmend automatisiert auf die zu produzierenden Werkstücke und Baugruppen ein. Wo früher die einzelnen Fertigungsprozesse Zuschneiden, Kanten, Schweißen sowie Lackieren transaktional, sequenziell und unabhängig voneinander abgearbeitet wurden, werden im neuen Werk alle Personen und Objekte immer enger in das Manufacturing Execution System (MES) eingebunden. Die Einzelbaugruppen werden am Ende automatisch zum fertigen Produkt zusammengeführt und mit einem QR-Code versehen, der eine Identifizierung auch in der späteren Weiterverarbeitung beim Kunden ermöglicht. Dabei kommunizieren die Maschinen und Handling-Systeme untereinander und mit übergeordneten Leitsystemen über Industrie-4.0-taugliche Kommunikationsnetzwerke. 20 fahrerlose Transportsysteme übernehmen automatisiert die Transporte im Werk.
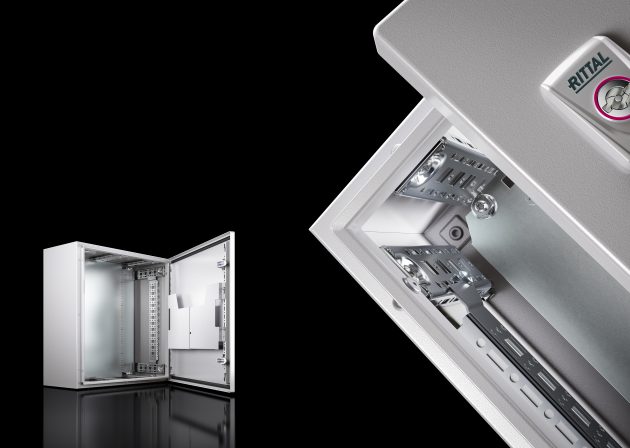
Zur Entwicklung des neuen Kompaktschaltschranks AX wurden aufwändige Studien und Kundenbefragungen durchgeführt.(Bild: Rittal GmbH & Co. KG)
Verschiebungen in der Arbeitswelt
Im Gespräch mit der anwesenden Fach- und Lokalpresse ging Friedhelm Loh auf die besonderen Aspekte ein, die es im Digitalisierungszeitalter bei der Errichtung einer neuen Produktionsstätte zu berücksichtigen gelte. „In der neuen Welt der Produktion sind die Investitionen sehr hoch. Wenn wir uns früher sehr intensiv mit Maschinen beschäftigt, sie installiert und betrieben haben, ist die Welt heute eine ganz andere: Es geht um Verknüpfung, es geht um Netzwerke, es geht um Daten“, betonte der Firmeninhaber. Mit Blick auf die Komplexität der neuen Fertigung für Kompaktschaltschränke und Kleingehäuse sagte Loh: „Diese Fabrik, in die wir investiert haben, ist ein Risiko. Das muss nicht klappen.“ Ohne Digitalisierung aber, so Loh, werde der Standort Deutschland auf Dauer nicht wettbewerbsfähig sein. Daher werde es eine Verschiebung zu mehr intelligenter Arbeit geben, woraus sich eine weitere große Herausforderung für die deutsche Industrie ableite: Zur Fortentwicklung und Behauptung in einem zunehmend umkämpften Wettbewerbsumfeld sei das lebenslange Lernen der Mitarbeiter noch nie so gefragt wie heute. Die Bereitschaft zur Aus- und Weiterbildung sei nicht mehr nur ein Kriterium, wenn man mit der Karriere vorankommen möchte, sondern eine essenzielle Überlebensfrage. Loh: „Wir haben bisher rund eine Million Euro allein darin investiert, dass die Mitarbeiter, die künftig hier in Haiger arbeiten werden, die neuen Maschinen und Prozesse verstehen. In früheren Zeiten wäre dies undenkbar gewesen. Heute gehört es dazu.“ Carsten Röttchen, Geschäftsführer Produktion bei Rittal, betont ergänzend, dass die Bereitschaft zur lebenslangen Aus- und Weiterbildung auch von Arbeitnehmerseite vorhanden sein müsse und gab dazu ein anschauliches Beispiel: „Der älteste fachfremde Mitarbeiter, der sich hier innerhalb eines Jahres zum IHK-zertifizierten Maschinen- und Anlagenführer hat ausbilden lassen, ist 55 Jahre alt. Dieser hat früher ausschließlich manuelle Tätigkeiten ausgeführt und arbeitet heute mit hoch komplexen Maschinen.“ Digitalisierung, so hob Uwe Scharf, Geschäftsführer Business Units und Marketing bei Rittal, hervor, dass Digitalisierung kein Selbstzweck sei, sondern nur dann Sinn mache, wenn dadurch die Wertschöpfungskette optimiert und die Wettbewerbsfähigkeit gestärkt werde. Mit Blick auf den Schaltanlagenbau bemerkte Scharf: „Digitale Daten werden Möglichkeiten eröffnen, an die wir heute noch gar nicht denken. So sind völlig neue digitale Service-Geschäftsmodelle im Bereich Instandhaltung, vorbeugender Wartung oder frühzeitiger Diagnostik denkbar.“
„Der deutsche Schaltanlagenbau ist internationale Spitze“
Interview mit Uwe Scharf, Geschäftsführer Business Units und Marketing bei Rittal
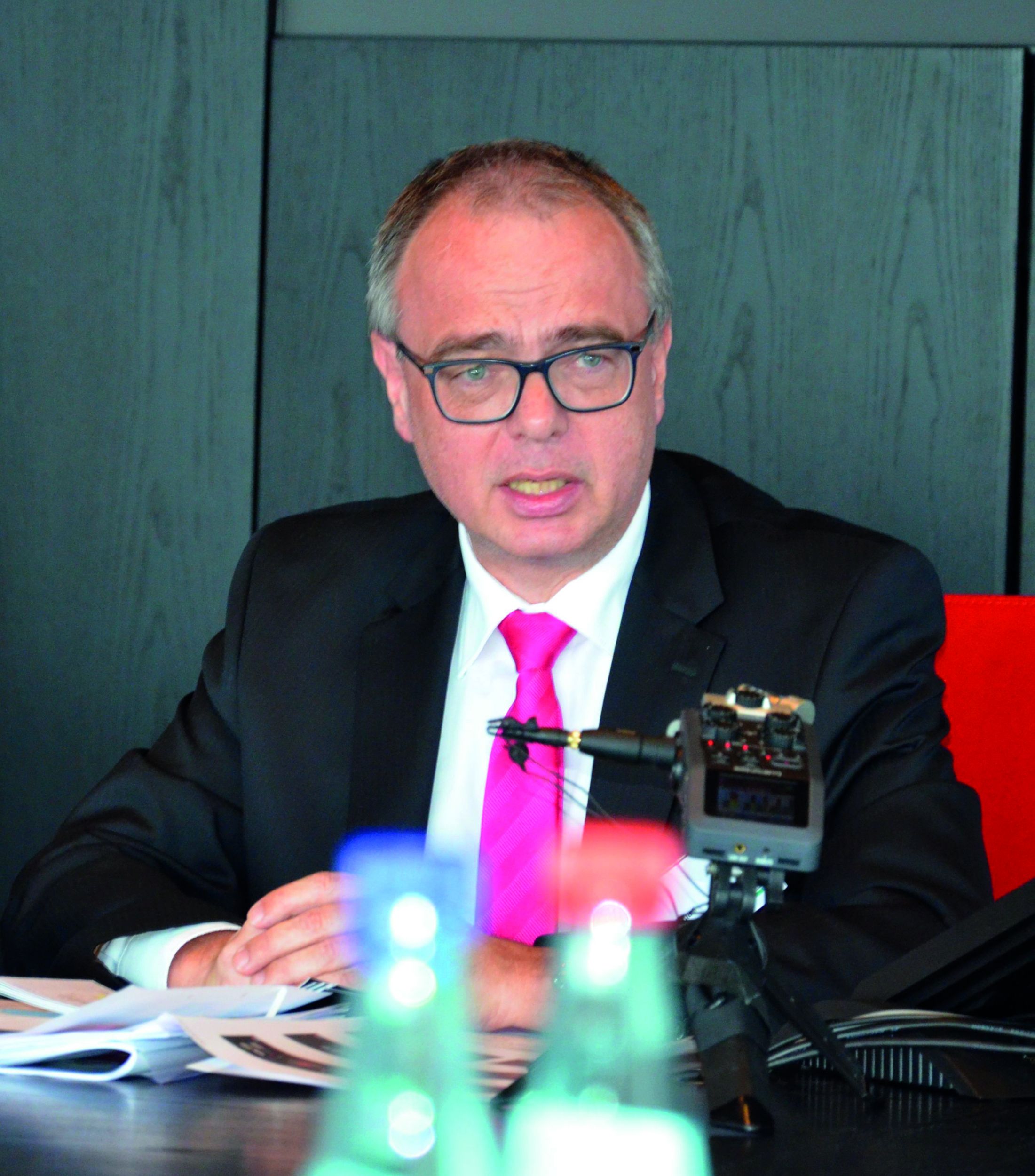
Uwe Scharf: „Der deutsche Schaltanlagenbau ist international gesehen absolute Spitze.“ (Bild: TeDo Verlag GmbH)
Herr Scharf, wurden bei der Entwicklung des neuen Kompaktschaltschranks AX ähnlich aufwändige Studien und Kundenbefragungen betrieben wie bei dem im letzten Jahr in den Markt eingeführten Großschranksystem VX25 oder wurden diese Verbesserungen weitestgehend vom einen System auf das andere transponiert?
Uwe Scharf: Das Optimierungspotenzial für das neue Produkt haben wir mit dem gleichen Kundenbeirat ermittelt, mit dem wir SSB beim VX25 bereits zusammengearbeitet haben. Wir denken uns tief in die Wertschöpfungsketten unserer Kunden ein, um die Arbeitsabläufe genauestens zu verstehen. Das beginnt bereits bei der Anlieferung unserer Produkte. Bei der neuen Baureihe führen die Erkenntnisse daraus zum Beispiel dazu, dass wir die Türen und Montageplatten unserer Schaltschränke nicht mehr vormontieren. Denn unsere Recherchen haben ergeben, dass etwa 80 Prozent der Schaltanlagenbauer nach Anlieferung der Schränke zunächst einmal die Türen demontieren, um z.B. Gravuren aufzubringen oder Schalter zu montieren. Gleiches gilt für die Montageplatte, die auch niemand im beengten Raum eines Gehäuses bearbeiten möchte. Das waren für uns wichtige Erkenntnisse. Bei einem Großschaltschrank wie dem VX25 konnten wir so allerdings nicht verfahren, da hier die montierten Türen und Montageplatten deutlich schwerer sind und durch den Verbau die Transportsicherheit sichergestellt wird.
Welche besonderen Herausforderungen hatten Sie bei Ihrer neuen Produktionsstätte hier in Haiger zu bewältigen?
Scharf: Die Taktraten hinzubekommen, bei denen schließlich im Optimum bis zu 9.000 Schränke pro Tag produziert werden sollen, war sicherlich die größte Herausforderung.
Wir haben es hier mit sehr komplexen verketteten Anlagen zu tun, wo, überspitzt gesagt, vorne ein Metall-Coil hineingefahren wird und hinten ein Schaltschrank herauskommt. Dabei läuft der Fertigungsprozess mit sehr geringen Puffern und sehr wenig manueller Arbeit ab. Die Produktion wird zentral von Leitrechnern gesteuert. 100 Einzelmaschinen, inklusive der Vernetzung sowie der hohen Taktraten: Das ist schon eine riesige Herausforderung. Wir optimieren jetzt noch die einzelnen Schritte und dieses Thema wird uns auch noch eine Weile begleiten. Das Zulieferkonzept erfolgt praktisch just in time mit minimalen Puffern. Der Warenausgang läuft ja jetzt direkt in unser Global Distribution Center, das heißt das GDC steuert letztendlich die Fabrik. Es kennt alle Aufträge, die europaweit reinkommen, weiß genau, was auf Lager ist und erteilt der Fabrik die Aufträge. Die Fabrik produziert, schiebt die Ware ins GDC und ordert gleichzeitig das Material, das benötigt wird, um weiter produzieren zu können. Da gibt es fast keine manuellen Planungsprozesse mehr. Entweder funktioniert die ganze Kette oder sie funktioniert nicht. Fehlerbehebung muss also sehr schnell und möglichst automatisch passieren. Das ist eben das Wesen der Vernetzung.
Mit Blick auf die Digitalisierung der Fertigung bei Ihren Kunden: Wo steht der Schaltanlagenbau im Frühjahr 2019? Gibt es bei Ihren Kunden noch große Diskrepanzen im Hinblick auf die Bereitschaft, Schritte hin zu mehr Digitalisierung einzuleiten bzw. umzusetzen? Gibt es z.B. einen Unterschied zwischen größeren und kleineren Betrieben?
Scharf: Zunächst einmal denke ich, dass der deutsche Schaltanlagenbau international gesehen absolute Spitze ist – und das betrifft sowohl die großen, als auch die kleineren Betriebe. Die Firmen, die nicht professionell aufgestellt sind, haben die letzten 20 Jahre hier in Deutschland nicht überlebt. Europa ist auch stark. In den USA wird die Industrialisierung gerade neu entdeckt. In Asien gibt es beide Extreme: hervorragende große Betriebe und einen Steuerungsbau, der absolut auf Weltniveau ist, es gibt aber auch das andere Extrem. Da ist der Markt sehr stark geteilt. Trotz des sehr guten Niveaus hier in Deutschland werden aber die Potenziale bei weitem noch nicht voll ausgeschöpft. Wir hatten nicht umsonst in unserem Innovation Center bisher mehr als 9.000 Besucher.
Das heißt der Beratungsbedarf unter den Schaltanlagenbauern ist sehr hoch?
Scharf: Absolut. Die Anzahl der Stunden für die Erstellung von typischen Schaltanlagen bewegt sich etwa zwischen 60 und 30, wobei letzterer Wert von nur wenigen Schaltanlagenbauern erreicht
wird. Ein Produktionsbetrieb kommt durch Optimierung aber nicht in einem Schritt von 60 auf 30 Stunden, sondern das geht in der Regel von 60 auf 50 Stunden, dann von 50 auf 35 und das Erreichen des Optimums wird dann immer schwieriger, da dies dann Investitionen in Maschinen, Software sowie die Aus- und Weiterbildung der Mitarbeiter erfordert. Um unseren Kunden den Weg zu erleichtern, werden wir gemeinsam mit unserem Schwesterunternehmen Eplan ein eigenständiges Consulting zur Optimierung der Wertschöpfungskette im Schaltanlagenbau aufbauen.