Drahtkonfektionierung im Steuerungs- und Schaltanlagenbau
Der direkte Draht
Die Automatisierung ist im Steuerungs- und Schaltanlagenbau ein aktuell heiß diskutiertes Thema. Was heute schon alles möglich ist, demonstriert das mittelständische Unternehmen Ripploh Elektrotechnik und Engineering. Hier konfektioniert etwa ein Wire Terminal die Drähte vollautomatisch. Und auch an der Verdrahtung mit Roboterunterstützung wird bereits gearbeitet.
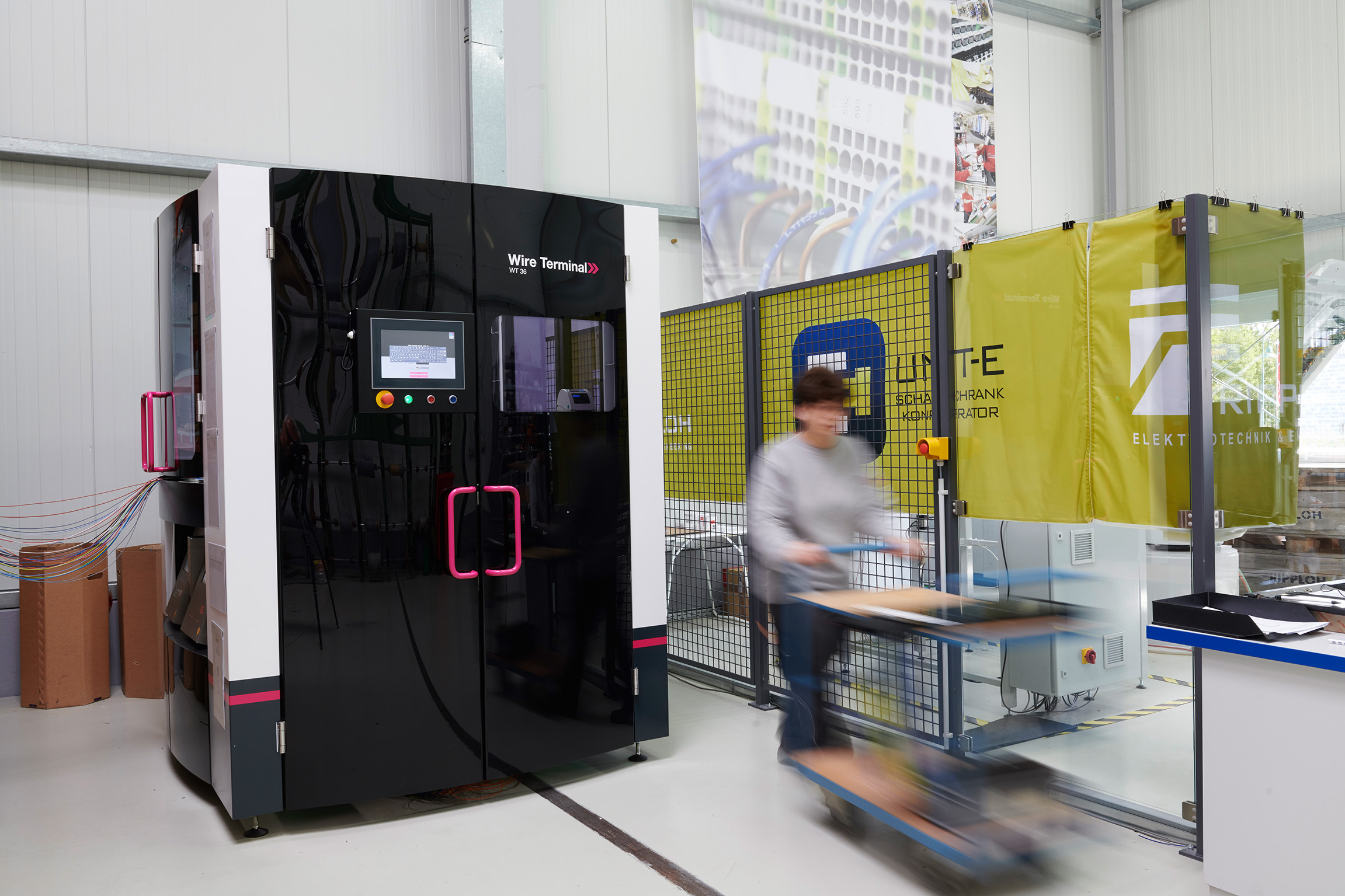
Die fertig konfektionierten Leitungen werden in die Werkstatt
transportiert, wo die Mitarbeiter sie dann im Schaltschrank verdrahten. (Bild: Rittal GmbH & Co. KG)
Eine große und aufgeräumte Werkstatt, in der zahlreiche Schaltschränke und Montageplatten auf die Weiterbearbeitung warten. Wenige Mitarbeiter sind konzentriert mit der Bestückung und Verdrahtung beschäftigt. Was außerdem sofort ins Auge fällt: Es gibt kein Papier – weder einen Ordner mit Schaltplänen noch Auftragszettel. Sieht so die Zukunft des Steuerungs- und Schaltanlagenbaus aus? Bei Ripploh Elektrotechnik & Engineering in Ostbevern ist diese Zukunft bereits heute Realität.
Saubere Datensätze sind entscheidend
Der Mittelständler aus dem Münsterland hat sich seit seiner Gründung 1995 von einem kleinen Auftragsfertiger mit vier Mitarbeitern zu einem Komplettanbieter entwickelt, der neben der Fertigung von Steuerungs- und Schaltanlagen auch das komplette Engineering anbietet. „Heute haben wir zahlreiche Kunden etwa aus dem Maschinenbau, die sich auf die Konstruktion ihrer Maschinen konzentrieren und uns lediglich die Art der verbauten Komponenten und die IOs vorgeben“, berichtet Andreas Ripploh: „Wir planen dann die gesamte Steuerungs- und Schaltanlage von Anfang an und fertigen diese dann in unserer eigenen Werkstatt.“ Sämtliche Prozesse bei Ripploh sind stark automatisiert. Das beginnt bereits in der Angebotsphase. „Ein Angebot ist ja schon ein Stück weit ein ‚Vorab-Engineering‘, in das wir auch eine Teil unseres Know-hows investieren müssen“, erklärt Ripploh. Für bereits vorgedachte und konfigurierbare Baugruppen stellt das Unternehmen deswegen den Schaltschrank-Konfigurator ‚Unit-E‘ (www.unit-e.de) bereit, mit dem der Kunde auf Basis der von ihm gemachten Angaben direkt ein Angebot erhält. Dem Konfigurator nachgelagert ist das Eplan Engineering Center (EEC). Dort wird nach einer Plausibilitätsprüfung mit der Detailplanung begonnen. Der Kunde erhält dann innerhalb von 24 Stunden den fertigen Schaltplan, in dem sämtliche Informationen enthalten sind. ‚Für die Angebotserstellung ist unser ERP-System eng mit Eplan verknüpft‘, erklärt Ripploh: „Wir pflegen sämtliche Komponenten-Daten in der Datenbank unseres ERP-Systems und schreiben diese dann direkt in die Eplan-Datenbank.“ Die Qualität der Daten und ein Datenformat mit einem einheitlichen Standard sind für den Unternehmer eine der wichtigsten Herausforderungen, an der in Zukunft noch viel gearbeitet werden muss: „Saubere Datensätze sind für den Steuerungs- und Schaltanlagenbau wichtiger als viele denken.“
Wire Terminal konfektioniert bis zu 36 unterschiedliche Drähte |
Der kompakte Drahtkonfektionier-Vollautomat Wire Terminal WT von Rittal macht die Verdrahtung wirtschaftlicher und effizienter. Ohne Umrüstung können je nach Typ bis zu 24 bzw. 36 unterschiedliche Drähte in den Querschnitten von 0,5 bis 2,5mm² vollautomatisch produziert werden. Die Arbeitsschritte Ablängen, Abisolieren und Crimpen erfolgen, ohne dass ein Mitarbeiter eingreifen muss. Das optional erhältliche Drucksystem kann die Drähte schwarz oder weiß bedrucken. Die Drähte werden mit dem gesteuerten Ordnungssystem an die nachgelagerten Prozessschritte übergeben. Das Ordnungssystem besteht aus einem 13-fachen Ablagesystem mit Drahtschienenmagazinen und kann bis zu 1.800 Drähte aufnehmen. Das Wire Terminal WT verfügt über Schnittstellen, über die Daten aus der Aufbauplanung mit Eplan Pro Panel nahtlos für die Konfektionierung der Drähte verwendet werden können. Alternativ kann der Bediener die Daten auch direkt an der Maschine manuell eingeben. Die fertig konfektionierten Drähte, die das Wire Terminal in dem Ordnungssystem ablegt, stehen für die Verdrahtung zur Verfügung. Das Wire Terminal WT kann die Drahtkonfektionierung im Steuerungsund Schaltanlagenbau um das 8-fache beschleunigen. Die vollautomatische Produktion garantiert dabei gleichzeitig eine kontinuierlich hohe Qualität. |
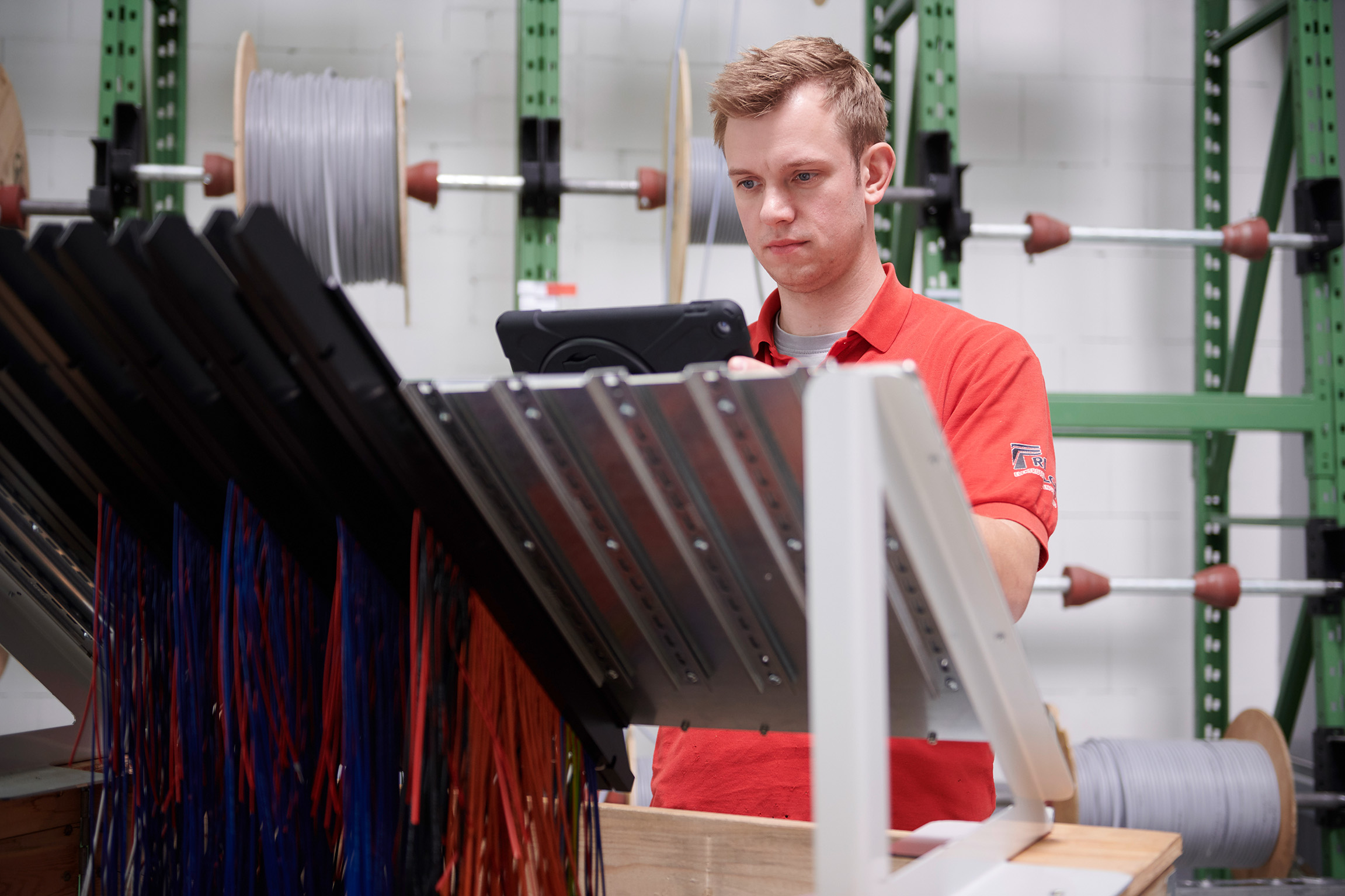
Alle Drähte für einen Auftrag werden in Schienen sortiert abgelegt und lassen sich so ideal weiterverarbeiten. (Bild: Rittal GmbH & Co. KG)
Drahtkonfektionierung viermal schneller
Die im Engineering erzeugten Daten werden bei Ripploh nahtlos dafür verwendet, um die Prozesse in der Werkstatt zu steuern. „Die 3D-Planung in Eplan Pro Panel liefert etwa die Daten für die CNC-Maschine zur Flachteilbearbeitung und für die vollautomatische Drahtkonfektionierung.“ Ablängen, Abisolieren, Crimpen und Beschriften der Leitungen übernimmt das Wire Terminal von Rittal Automation Systems. Bis zu 1.500 Drähte kann die neue Maschine innerhalb einer 8-Stunden-Schicht konfektionieren. Und da, nachdem ein Auftrag gestartet wurde, kein Eingriff eines Bedieners mehr notwendig ist, produziert das Wire Terminal über Nacht nochmals die gleiche Menge. „Der Mitarbeiter kann morgens die Drähte aus der Maschine entnehmen und direkt mit dem Verdrahten beginnen“, erklärt Ripploh. Im Vergleich zur alten Lösung steigt die Produktivität bei der Drahtkonfektionierung dadurch um das Vierfache, und zudem ist nicht ständig ein Mitarbeiter notwendig, um die Maschine zu bedienen.
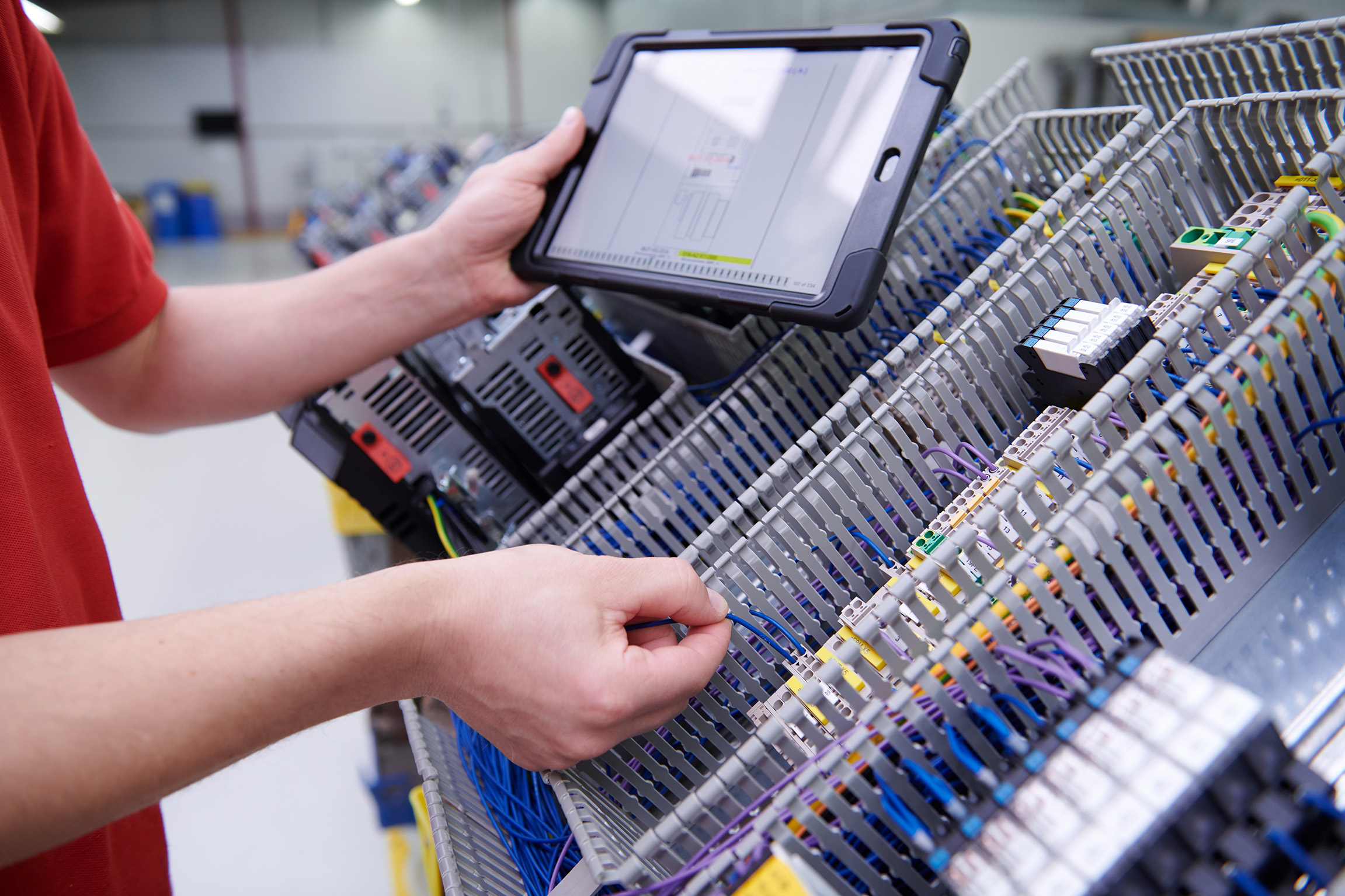
Papierlose Fertigung ist bei Ripploh Standard – Über iPads lassen sich alle notwendigen Informationen zu den Aufträgen abrufen. (Bild: Rittal GmbH & Co. KG)
Arbeitsabläufe exakt geregelt
Für den Firmenchef hat das Wire Terminal aber noch einen weiteren entscheidenden Vorteil: „Die Sequenz – also die Reihenfolge, in der die Drähte konfektioniert und in den Schienen abgelegt werden, – können wir jetzt vorgeben.“ Diese Funktionalität ist sehr wichtig für die Effizienz der Verdrahtung. Wenn beispielsweise eine Kleinserie mit zehn Schaltschränken verdrahtet wird, kann die Reihenfolge so gewählt werden, dass der Mitarbeiter den gleichen Draht in allen Schränken nacheinander verdrahtet. Da er den Ablauf nach dem ersten Schaltschrank kennt, geht die Arbeit bei den übrigen Schaltschränken deutlich schneller. Wird dagegen beispielweise ein Steckverbinder mit fünf Leitungen angeschlossen, kann es sinnvoller sein, in jedem Schaltschrank zunächst die fünf Leitungen zu verdrahten, bevor mit dem nächsten Schaltschrank fortgefahren wird. „Wir können so die Verdrahtungsabläufe genau vorgeben, was die Arbeit zusätzlich effizienter macht“, ist sich Ripploh sicher. Das Wire Terminal fügt sich somit nahtlos in den ausgeklügelten Workflow in der Werkstatt ein.
Auf Herz und Nieren geprüft – und weiterentwickelt |
Um das neu entwickelte Wire Terminal von Rittal, das erstmalig auf der SPS IPC Drives 2018 vorgestellt wurde, unter realen Anwendungsbedingungen im Steuerungs- und Schaltanlagenbau zu testen, wurde es 2019 einem Betatest bei Ripploh Elektrotechnik und Engineering unterzogen. Mit Unterstützung des Anlagenbauers erfolgte eine Weiterentwicklung des Kabelkonfektionierautomaten. „Wir freuen uns sehr, dass wir mit Andreas Ripploh einen langjährigen, guten Kunden und Mitglied des Kundenbeirats schon in der Betatest-Phase des Wire Terminals gewinnen konnten, um gemeinsam die notwendigen Schritte in der Praxis zu gehen und die Drahtkonfektionierung mit der Innovationsstärke seines Unternehmens auf ein noch höheres Niveau zu heben und prozesssicher zu gestalten”, sagt Tim Kramer, Abteilungsleiter Automation Systems bei Rittal. |
Tablet statt Auftragszettel
Im Weiteren liegen Betriebsaufträge bei Ripploh nicht in Form von Auftragszetteln auf Papier vor, sondern jeder Mitarbeiter hat ein iPad, das ihn mit den Aufträgen und allen notwendigen Informationen versorgt. Schaltschränke, kommissionierte Komponenten und jetzt auch die Magazine mit den über das Wire Terminal konfektionierten Drähten sind mit QR-Codes versehen. Der Mitarbeiter scannt den QR-Code mit seinem iPad und kann dann den Auftrag abarbeiten. „Die Anbindung an das ERP-System und an das Engineering ist auf diese Weise stets aktuell“, erklärt Ripploh: „Nur wenn auf dem Server die freigegebenen Pläne vorliegen, kann der Mitarbeiter beispielsweise mit dem Verdrahten beginnen.“ Auf seinem Bildschirm bekommt er u.a. die Verlegewege für die Verdrahtung angezeigt. Dies sorgt nicht nur für eine hohe Effizienz und Geschwindigkeit, sondern gleichzeitig wird die Wahrscheinlichkeit für Fehler stark reduziert. Änderungen, die trotz sorgfältiger Planung immer mal vorkommen können, kann der Mitarbeiter mit einem Stift direkt in der PDF-Datei des Schaltplans auf dem iPad eintragen. Diese Methode entspricht dem klassischen Redlining, bei der Änderungen im ausgedruckten Schaltplan markiert werden. Durch die Digitalisierung ist es jetzt aber möglich, dass die vorgenommenen Änderungen auch den Weg zurück ins Engineering finden. Dadurch ist garantiert, dass der fertige Schaltschrank und der dann aktualisierten Schaltplan exakt übereinstimmen.
Gehört die Zukunft dem Roboter?
Mit der umfangreichen Automatisierung und Digitalisierung hat der Steuerungs- und Schaltanlagenbauer schon viel erreicht, meint der Firmenchef: „Wir können heute mit der gleichen Anzahl an Mitarbeitern deutlich mehr Aufträge abwickeln als noch vor ein paar Jahren.“ Das ist vor allem deswegen wichtig, da qualifizierte Fachkräfte auf dem Arbeitsmarkt praktisch nicht zur Verfügung stehen. Da die gesamte Digitalisierung die Tätigkeiten in der Werkstatt sehr restriktiv vorgibt, ist es außerdem möglich, dass auch angelernte Mitarbeiter einen Teil der Aufgaben übernehmen. Die Automatisierung im Steuerungs- und Schaltanlagenbau ist nach Meinung von Andreas Ripploh noch lange nicht abgeschlossen: „Der nächste Schritt wird wahrscheinlich die automatisierte Verdrahtung sein.“ Da das Wire Terminal die konfektionierten Drähte in seinen Ordnungsmagazinen definiert ablegt, ist eine Übergarbe an einen Roboter, der dann die Verdrahtung durchführt, durchaus denkbar. „Wir arbeiten bereits daran und sind überzeugt, dass wir in etwa zwei Jahren mit Unterstützung eines Roboters verdrahten können“, wagt Ripploh einen Blick in die Zukunft.